Robotic micromanipulation station
Integration of a device on an industrial robot to micromanipulate submillimetric objects
Centralization and development of control/execution and the Human/Machine Interface on a computer by using LabVIEW
Hardware architecture
Presented at the MICRONORA trade show, the micromanipulation station is composed of the following elements:
- A RP-1AH industrial robot linked to a CR1 controller unit and a R28 TB Teach Pendant;
- A LEMMOC-type microgripper developed in the lab (in-house), and its high voltage interface;
- A Barebone-type computer equipped with an acquisition card (National Instruments ref. PCI-6733) to pilot the microgripper, linked by a serial RS-232C protocol to communicate with the robot control unit;
- Several compliant tables offer a safe workplace environment to prevent microgripper collisions;
- A two-camera vision system (above and side views) and a screen for operator real-time monitoring of the micromanipulation tasks.
Software architecture
The software architecture is based on two applications following a master/slave mode. The slave program in the robot control unit is coded in Melfa Basic IV and awaits orders from the master application. Developed with Labview® 7.1 (National Instruments), the master program transmits the necessary information to the robot control unit and to the microgripper. The operator obtains the following functionalities:
1. Station calibration
It is carried out once, and allows for reliable trajectory programming while preventing microgripper collisions with its environment. Calibration requires the following two steps:
- Numerically set the tool-end coordinates for the microgripper on its base to enable move commands according to the teach point and not according to the robot base;
- Numerically set point coordinates according to the robot base. This allows the slave program to block move commands, which would place the tool in lower position compared with the determined point.
All parameter values are transmitted from the computer to the robot control unit, which the slave program controls while in operation.
2. Remote micromanipulation of submillimetric samples
This functioning mode allows the operator to use the keyboard to pilot the robot tool by incremental moves, both x and y translation and axial rotation (J4). It also allows moving the microgripper, by both opening and closing the finger-like structures, and moving them upwards and downwards. Each of the 4 incremental motions can be configured on the graphic interface from the keyboard and/or the mouse. The robot and microgripper finger trajectories are carried out using linear interpolations, according to position for the robot and to tension for the microgripper.
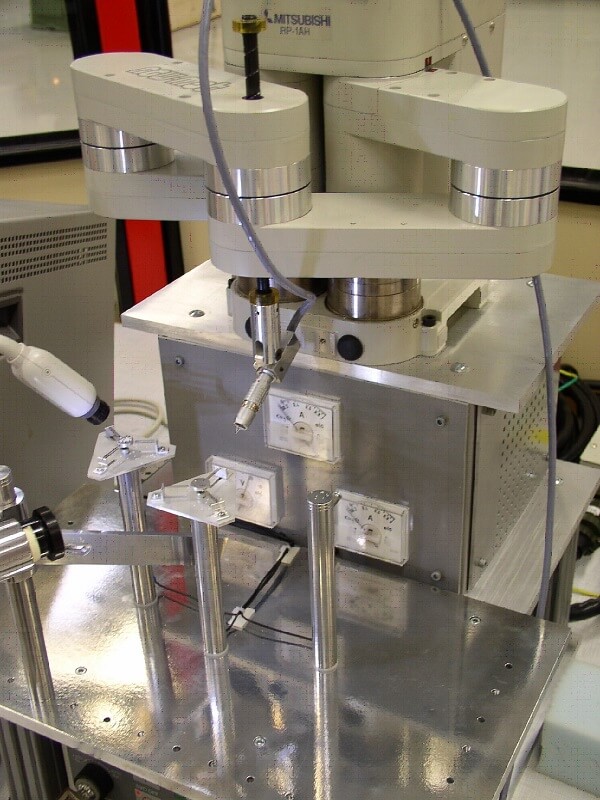
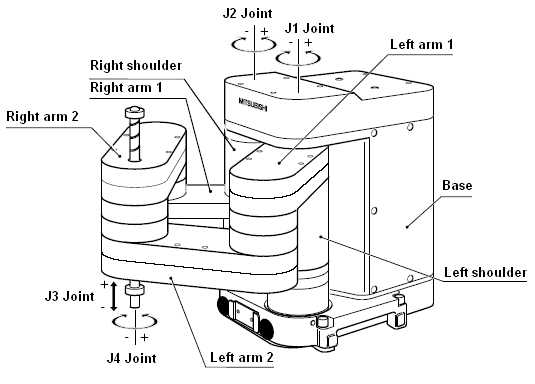
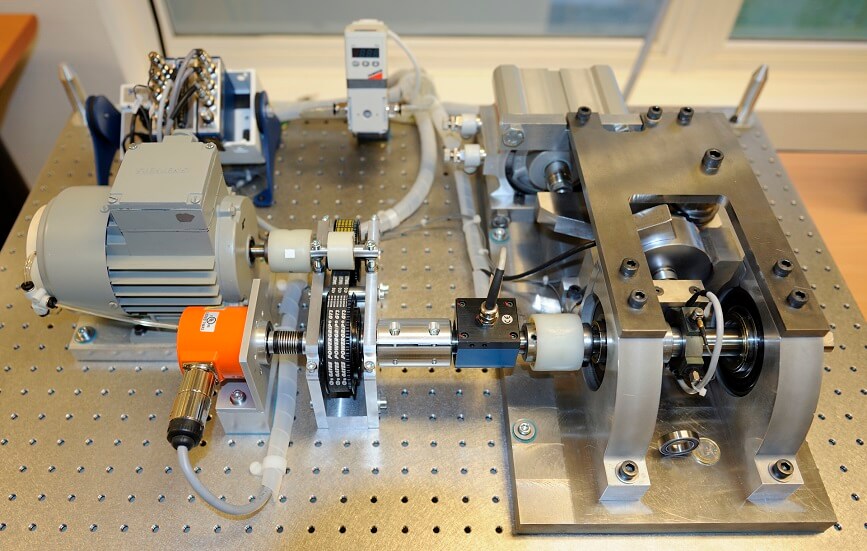